Автоматическое тестовое оборудование с подвижными пробниками в производстве электронных изделий
Необходимость изготовления тестовых адаптеров для каждого изделия является серьезным недостатком, ограничивающим применение электрического тестирования электронных изделий на стадии производства. Для предприятий с мелкосерийным многономенклатурным производством (коих в России большинство) применение такой технологии вообще невозможно. Тем не менее, очень часто требуется выпускать продукцию, имея крайне ограниченное время на ее тестирование и контроль. Где же выход?
При электрическом тестировании электронных изделий на стадии производства долгое время применялись системы с тестовыми адаптерами типа "поле контактов" (bed-of-nails). Такой метод обеспечивает одновременный доступ ко всем цепям тестируемого изделия и, соответственно, высокую производительность контроля. Никто не оспаривает необходимости адаптерного тестирования в случае серийного производства продукции или выпуска электроники ответственного назначения. Однако серьезным недостатком, ограничивающим применение такой технологии, является необходимость изготовления тестовых адаптеров для каждого изделия, что приводит к дополнительным финансовым затратам и потере времени при освоении новых изделий. Для предприятий с мелкосерийным многономенклатурным производством, каковыми является большинство предприятий в России, применение такой технологии вообще невозможно. Отметим, что использование адаптеров предъявляет к проверяемым платам ряд повышенных требований по тестопригодности (наличие и размер тестовых площадок или переходных отверстий), которые часто просто невозможно выполнить на современных платах с высокой плотностью монтажа. Кроме того, просматриваемая в последнее время тенденция производства все более сложных электронных изделий приводит к росту входов/выходов и повышению плотности монтажа. В таких электронных изделиях широко используются гибридные микросхемы, BGA, µBGA, Flip Chip, CSP, ASIC, компоненты поверхностного монтажа (SMD), планарные трансформаторы и т. д. Понятно, что при всем этом требуется и высокая надежность изделий, которая ужесточается в случае производства электронной продукции оборонного назначения, выпускаемая небольшими сериями при огромном количестве модификаций. Можно также добавить, что очень часто требуется выпускать изделия в самые сжатые сроки, имея крайне ограниченное время на их тестирование и контроль.
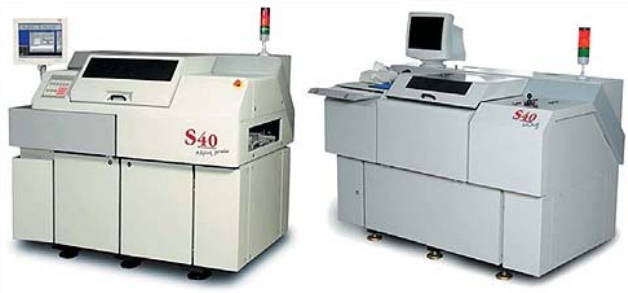 Рис. 1. Тестеры с подвижными пробниками S40 Pilot и S40 PilotLX
Именно в таких случаях на помощь приходят тестеры электрического контроля с подвижными или "летающими" пробниками (Flying Probe Tester = FPT). В данной статье пойдет речь о тестере с подвижными пробниками S40 PILOT итальянской фирмы SEICA, часто реализуемым под торговой маркой мирового лидера тестового оборудования - американской компании Teradyne.
Место тестера в общей стратегии тестирования
Приведем таблицу, рассмотренную в предыдущей статье автора ("Автоматическое тестовое рентгеноскопическое оборудование в производстве электронных изделий", "КиТ" N 9'2004).
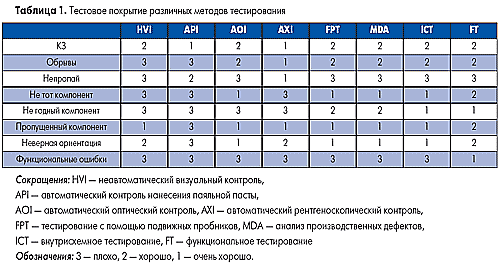
Хорошо известно, что ни один из представленных в таблице 1 методов тестирования не позволяет обнаруживать 100% дефектов на выпускаемом электронном изделии. Поэтому необходимы новые тестовые стратегии, сокращающие время разработки тестового ПО и обеспечивающие быстрый и эффективный цикл ввода новой продукции в производство, предоставляя при этом высокий уровень выявляемости дефектов еще на стадиях разработки продукции. Для освоения новых видов продукции рекомендуются бесконтактные тестовые методы (неэлектрический контроль), такие как автоматический оптический (AOI) и рентгеноскопический контроль (AXI), а также автоматическое тестовое оборудование с подвижными пробниками (FPT), дающие высокий процент обнаружения брака и быстрое внедрение без дополнительных расходов и издержек на контактные устройства (адаптеры).
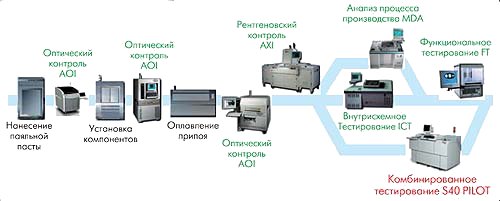 Рис. 2. Тестовое оборудование в производственной линии
Для подтверждения правильности выбора той или иной стратегии тестирования применяется специализированное программное обеспечение, предназначенное для его проектирования - DfT (Design-for-Test). Наиболее известной программой такого рода является фирменный продукт Strategist американской компании TERADYNE. Эта программа дает пользователям возможность разрабатывать оптимальные стратегии тестирования, которые способны максимально увеличить покрытие ошибок и эффективность контроля, ускорить выход на рынок качественного нового изделия и сократить время достижения планируемого объема производства (см. табл. 2). Полученный уровень разработки стратегий тестирования убеждает, что моделирование спектра дефектов и выявляемости дефектов для каждого вывода компонента, позволяют оптимизировать тестовое покрытие всего изделия и производительность. Программа Strategist анализирует конструкцию платы, моделирует конфигурацию производственной линии, оптимизирует стратегию контроля и тестирования. Это исключает ручную работу при распределении этапов тестирования и экономит большое количество производственного времени. Прозрачная архитектура программного обеспечения Strategist позволяет разрабатывать стратегию тестирования с учетом применения в ней 2D/3D-рентгеноскопических систем, AOI, внутрисхемных и функциональных тестеров, универсальных тестеров с подвижными пробниками, а также анализаторов производственных дефектов, независимо от поставщика оборудования. Другими словами, в оптимизированной с помощью Strategist стратегии тестирования может быть использовано тестовое оборудование от разных фирм производителей. Strategist позволяет найти оптимальное тестовое решение для технологий производства сложных электронных блоков в условиях ограниченного физического доступа к их электрическим цепям при тестировании.
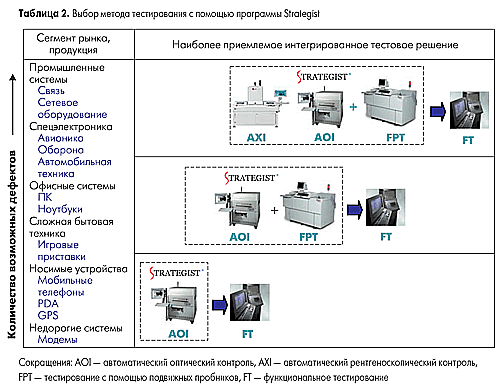
Как было отмечено выше, безадаптерные методы тестирования наиболее предпочтительны при освоении новых изделий. Поэтому в данном случае весьма эффективной является стратегия, которая объединяет использование методов AXI и AOI с методом FPT. Метод AXI используется для проверки качества сборки, а FPT обеспечивает электрическое покрытие ошибок. Так как оба метода безадаптерные, высокий уровень покрытия ошибок может быть получен за короткий период времени (по сравнению с методом ICT). Время для проверки обрывов и КЗ методом FPT часто является помехой при тестировании плат с большим количеством электрических цепей. Однако в сочетании с автоматическим AXI и AOI время верификации обрывов и КЗ методом FPT может быть значительно уменьшено, так как программа Strategist может спрогнозировать, какие обрывы и КЗ протестируются AXI + AOI, и поэтому не потребуют подтверждения FPT. Существенно сокращается число цепей, которые необходимы для зондирования во время тестирования обрывов и КЗ, что, в свою очередь, сокращает время работы методом FPT. В этом случае обеспечивается возможность бездефектного производства электронных модулей в условиях среднесерийного производства.
Обращаем особое внимание, что в качестве AXI-системы в таблице 2 может быть использована лишь встраиваемая в производственную линию автоматическая рентгеноскопическая система. По имеющимся у авторов данным, единственная удовлетворяющая указанным характеристикам AXI-система - XStation HS, производимая американской фирмой Teradyne. В качестве показательного примера применения встроенного в производственную линию AXI может служить его использование на производстве известной американской компании HMG. Номенклатура сложных электронных изделий данной фирмы содержит около 125 позиций. Средний объем производимой продукции при 7-дневной рабочей неделе с двухсменным графиком работы - приблизительно 10000 изделий в неделю. Среднее время тестирования электронного модуля (примерно 200 электронных компонентов) системой XStation HS составляет 20-30 секунд. За это время на каждом проверяемом модуле при фактически 100%-ном тестовом покрытии осуществляются следующие тесты:
- обрывы и КЗ;
- избыток и недостаток припоя на компонентах;
- отсутствие компонента;
- перекос компонента;
- контроль пайки микросхем в корпусах QFP, SOP, BGA, CSP и т.д.
Отметим, что использование в производственных линиях наиболее известных производителей электроники именно тестеров AXI позволяет поддерживать высочайшее качество выпускаемой продукции - на уровне 5-8 ppm (количество отказов на миллион изделий).
Особенности тестера с подвижными пробниками S40 PILOT
Тестер с подвижными пробниками имеет несколько тестовых головок с приводами по осям X, Y и Z. Тестовые головки (обычно четыре) перемещаются над испытываемой платой с большой скоростью. В это время электрические зонды ("подвижные пробники"), расположенные на каждой головке, вступают в контакт с переходными отверстиями и контактными выводами каждого устройства, расположенного на плате. Таким образом обеспечивается последовательный доступ к контрольным точкам тестируемого изделия.
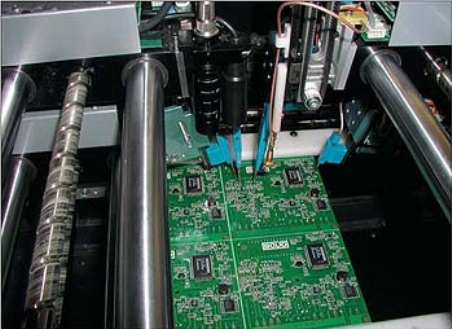 Рис. 3. Работа тестера S40 Pilot с мультиплтцтрованной заготовкой
Некоторые технические характеристики тестера:
- - Быстродействие тестера - 70000 компонентов/с.
- - Шаг между контактными площадками - до 0,4 мм.
- - Минимальный размер контактной площадки состовляет 0,18 x 0,18 мм.
- - Рабочая область: 400 x 600 мм (610 x 610 мм для модели LX).
- - Максимальная высота компонентов 70 мм (со стороны подвижных пробников).
Отметим, что помимо четырех подвижных пробников, осуществляющих тестирование с верхней стороны платы, тестер имеет восемь фиксированных пробников, обеспечивающих контактирование с контрольными точками, расположенными с нижней стороны тестируемой платы. Количество фиксированных пробников (каналов) может быть увеличено до 1024, что позволяет тестировать сложную электронику через краевой разъем.
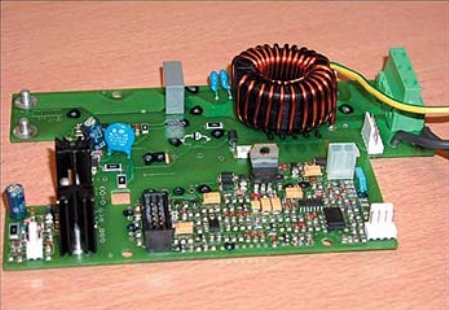 Рис. 4. Образец тестируемого на S40 Pilot электронного модуля (128 компонентов, 86 цепей). Время тестирования - 30 сек.
Система S40 PILOT позволяет осуществлять следующие тесты:
- аналоговое тестирование или анализ производственных дефектов (MDA): короткие замыкания, обрывы цепей, номиналы резисторов, конденсаторов и индуктивностей, полноценная проверка полупроводниковых компонентов (диодов, стабилитронов, транзисторов), проверка трансформаторов и реле, а также выполнение многопроводных измерений. Расстановка блокирующих напряжений (guards) при создании тестовых программ выполняется автоматически.
- Внутрисхемное цифровое тестирование цифровых микросхем.
- Функциональное тестирование элементов, узлов, изделия в целом с подачей на тестируемое изделие питающего напряжения.
- Оптический видеоконтроль (AOI).
- Периферийное сканирование (Boundary Scan).
- Контроль качества пайки выводов поверхностно монтируемых микросхем в корпусах PLSS, QFP, BGA, SO с помощью комплекта емкостных пробников (2 подвижных сверху, 16 фиксированных снизу).
Требования к тестопригодности контролируемых изделий
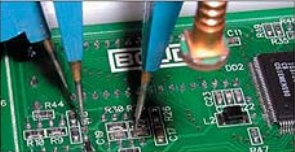 Рис. 5. Контактирование пробника S40 Pilot (3-й слева) с установочной площадкой резистора
Одной из наиболее сильных сторон тестера с подвижными пробниками по сравнению с обычными адаптерными тестовыми системами является возможность тестирования сложных электронных изделий в условиях пониженных требований к их тестопригодности. Отметим, что, согласно рекомендациям Международного комитета по проблемам тестопригодности (SMA TESTABILITY COMMITTEE) для разработчиков электронных изделий, для эффективного использования автоматизированного тестового оборудования (ATE), обеспечивающего надежное контактирование тестируемых изделий с тестовым адаптером и точную локализацию возможных дефектов, необходимо гарантировать надежное контактирование тестовых пробников с тестируемым изделием. В случае применения тестовых адаптеров контактирование пробников должно осуществляться на специальные контактные площадки или в незакрытые маской переходные отверстия. Если эти условия не выполняются или выполняются не полностью, такие электронные изделия считаются полностью или частично нетестопригодными. Во многих случаях тестеры с подвижными пробниками позволяют обходить эту проблему, так как допускают контактирование подвижных пробников с установочными контактными площадками ПМ ИЭТ (поверхностно монтируемые изделия электронной техники). Заметим, что при этом не допускается их контактирование с выводами ПМ ИЭТ, так как контактное давление пробников может привести к прижатию непропаянных или не припаянных контактных выводов компонентов к контактным площадкам, маскированию дефектов "холодной пайки" и т. д.
Продолжение следует.
Игорь Марков, Игорь Рыков
|